Industrielle Automatisierung
Vorbereitung auf die Industrie 4.0 mit IO-Link-Technologie
22.06.2021
Ob bereit oder nicht, Industrie 4.0 ist bereits Realität. Die Fertigung wird zunehmend digitalisiert und automatisiert, wobei Technologien wie Big Data, Augmented und Virtual Reality sowie Robotik zum Einsatz kommen.
According to a recent report from McKinsey, companies can expect gross-margin increases of 30% in just two years by deploying digital tools like automation and analytics.
Behind the scenes, acting as the enabler of Industry 4.0, is IO-Link. As a simple, point-to-point communication protocol, IO-Link connects sensors and actuators with an IO-Link Master, which then converts those signals to an industrial Ethernet message. This technology can be utilized in factory and logistics automation environments.
IO-Link transforms traditional sensors into “smart” sensors so they can communicate to more than one single parameter. Instead of reporting only a “low” or “high” signal for example, a sensor utilizing IO-Link protocol can relay the actual temperature value in real-time.
To deploy IO-Link, a single cable is run from an IO-Link device (a sensor or actuator) to an IO-Link master that transmits data from the field I/O level via Ethernet to a PLC or cloud system.
As manufacturing applications become more automated, demands are changing for the IO-Link masters that collect digital inputs and outputs or IO-Link signals and convert the data into a fieldbus or IIoT protocol.
Here’s what we’ve noticed in terms of increasing demands for IO-Link masters:
1. More Emphasis on Monitoring & Maintenance
Quality monitoring (examining a manufactured component’s dimensions, weight and appearance) and predictive maintenance (tracking real-time equipment health, status and performance) are extremely valuable in a variety of manufacturing settings to reduce costs, prevent unexpected downtime and make better use of labor.
Consider photoelectric switches with lenses, for example. You may want the sensor to not only indicate whether it can detect an object, but also indicate when its lens is dirty enough to warrant cleaning. Having that information provided in real-time eliminates the hassle of assigning an employee to clean the sensor every hour or two, saving valuable labor resources and money so you can redirect staff to other critical tasks.
This type of additional information can be transmitted via IO-Link through an IO-Link master to a PLC or cloud system enabling new predictive maintenance services which were not previously available.
2. Faster Cycle Times
IO-Link allows remote monitoring of sensor signals and status alerts to quickly identify and resolve problems before they lead to downtime.
Automation speed plays a crucial role in optimization of manufacturing processes. IO-Link masters now need to keep internal latency times so low that cycle times of around 1 millisecond are possible to ensure that IO-Link data is forwarded to the PLC quickly.
Belden's older IO-Link masters have cycle times of around 7 milliseconds; however, our newer IO-Link masters can achieve cycle times that are up to seven times faster than previous generations.
3. Reliance on More Fieldbus and IIoT Protocols
Different fieldbus protocols are being used across plants to support integration. Trends such as small batch sizes and customized/individualized requests require more flexibility and automation—as well as connections to various fieldbuses and IIoT applications.
IO-Link is fieldbus and vendor neutral: It can connect to existing fieldbus protocols, such as PROFINET, EtherCAT, EtherNet/IP and Modbus TCP. Multiprotocol IO-Link masters can support connectivity to one of these four these fieldbus protocols for fast, reliable data transmission to the PLC environment.
They also offer the ability to choose from different IIoT direct-communication protocols—like OPC UA, MQTT, CoAP, and REST API—to foster direct communication between the cloud and the sensors at the field level.
4. Increased Power Needs
Current output is also on the rise as applications call for more power. Some IO-Link masters may be limited to providing 500 mA of output current per port. Our new, state-of-the-art IO-Link masters, however, can offer up to 2 A of output current per port to support emerging technology and new applications without the need for additional power supply, important for larger actuators.
5. Improved Protection and Security
Security is most effective when it operates in a pyramid, offering protection from the top down.
For the first time, our IO-Link masters are now able to offer security clear down to the field level: sensors, actuators and IO-Link devices. This ensures that safe remote maintenance and diagnostics can be achieved without worry of data manipulation or unauthorized system use.
Meet LioN-X®: A New IO-Link Master Solution 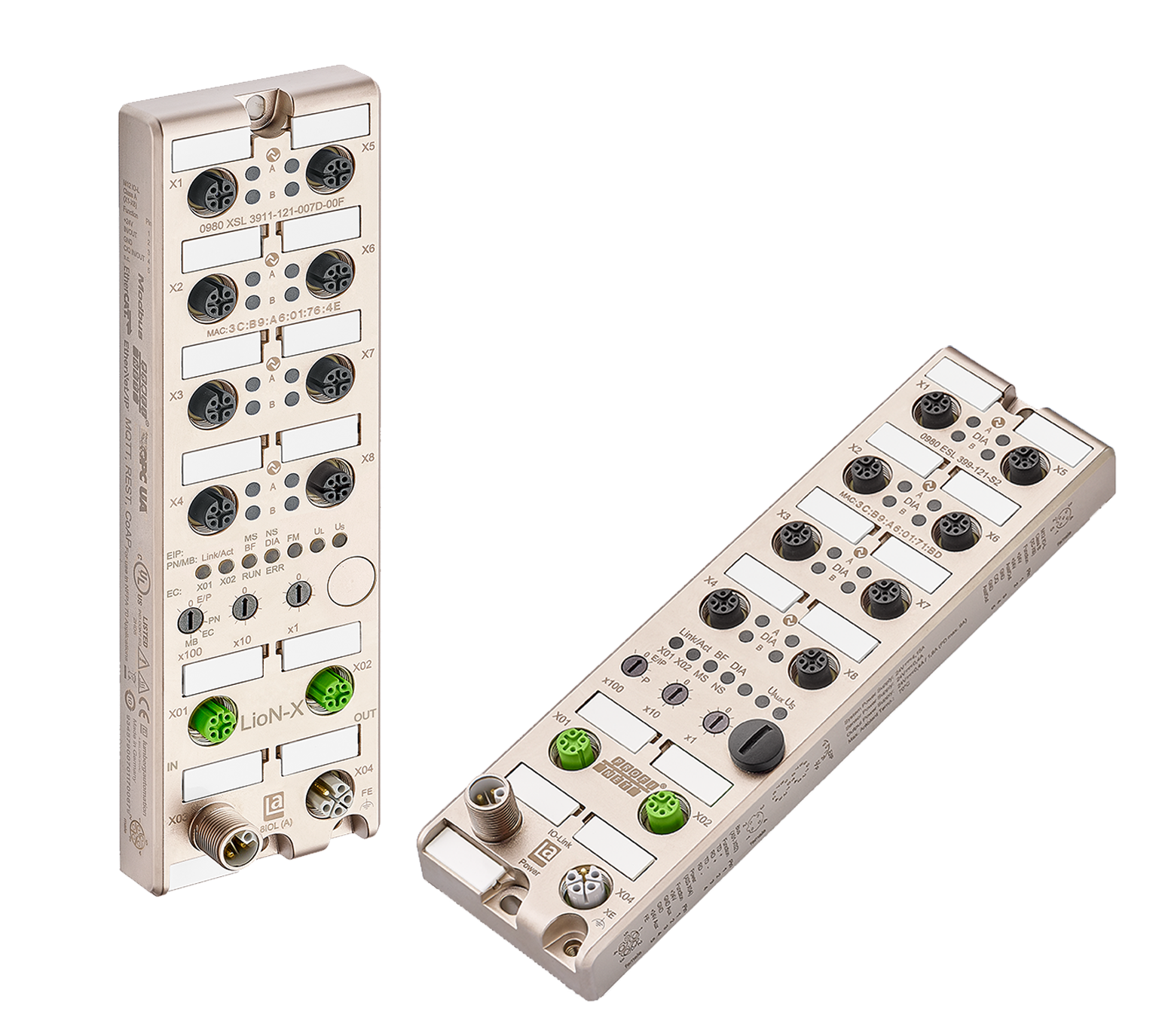
The new LioN-X family from Lumberg Automation combines IO-Link masters and I/O modules with one-of-a-kind features not found in other IO-Link masters, including support of OPC UA communication protocol, ACHILLES-certified security features and current output of up to 2 A per port.
With several IIoT and Ethernet based fieldbus protocols on board, LioN-X IO-Link masters are a fast, reliable and secure solution to collect, convert and transmit critical data in automated production environments. Because of their flexibility and versatility, they can be used in nearly any factory automation or logistics automation setting.
The new product family includes LioN-X and LioN-Xlight, which is a highly cost-effective alternative to the full LioN-X solution. It comes equipped with only the most vital features for applications that may not need full-feature options, such as security. Solutions within the LioN-X family can also be customized for any environment.
Want to learn more about working with Belden to implement IO-Link technology to improve operations in factory and logistics automation environments? Download our IO-Link white paper!